ABOUT MEG
Walking Together, Growing Together
MIYAJI ENGINEERING GROUP (MEG) continues to
contribute to the enrichment of our nation and the creation of
a brighter society through the construction, maintenance, and repair of
societal infrastructure such as bridges, buildings, and coastal structures.
Here is an introduction to our business.
About Us
MEG is one of the most comprehensive engineering companies in the bridge industry. With MIYAJI ENGINEERING CO., LTD. (MEC) and MM BRIDGE CO., LTD. (MMB) as our main operating subsidiaries, our combined capabilities span four areas: advanced design for maintenance and repair work, including new construction and large-scale renewal of steel bridge such as long-span bridges and railroad bridges; manufacturing technology; construction planning, and on-site safety construction.
We are also a comprehensive engineering company for steel structures. We can construct large-space and specialized buildings such as towers and domes, which require advanced technical capabilities, and design and manufacture coastal structures such as immersed tube tunnels and caissons.
As a contributor to social infrastructure development, MEG will ensure the safety and security of the public and help build an affluent society through the construction, maintenance and repair of bridges and other special structures, while striving for sustainable development for the future.
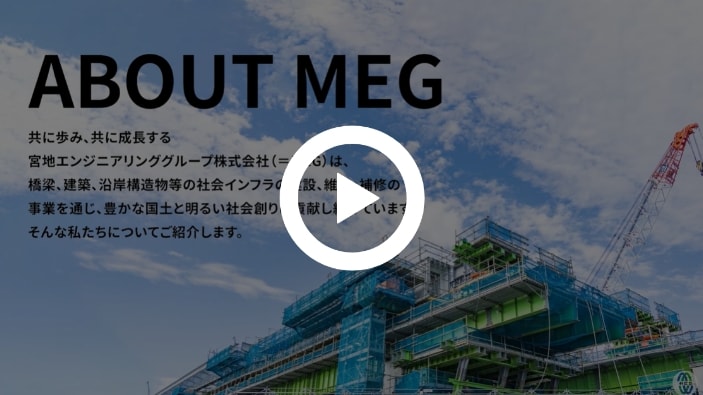
Commemorative Issue Celebrating the 115th Anniversary of Our Founding and the 20th Anniversary of Our Establishment

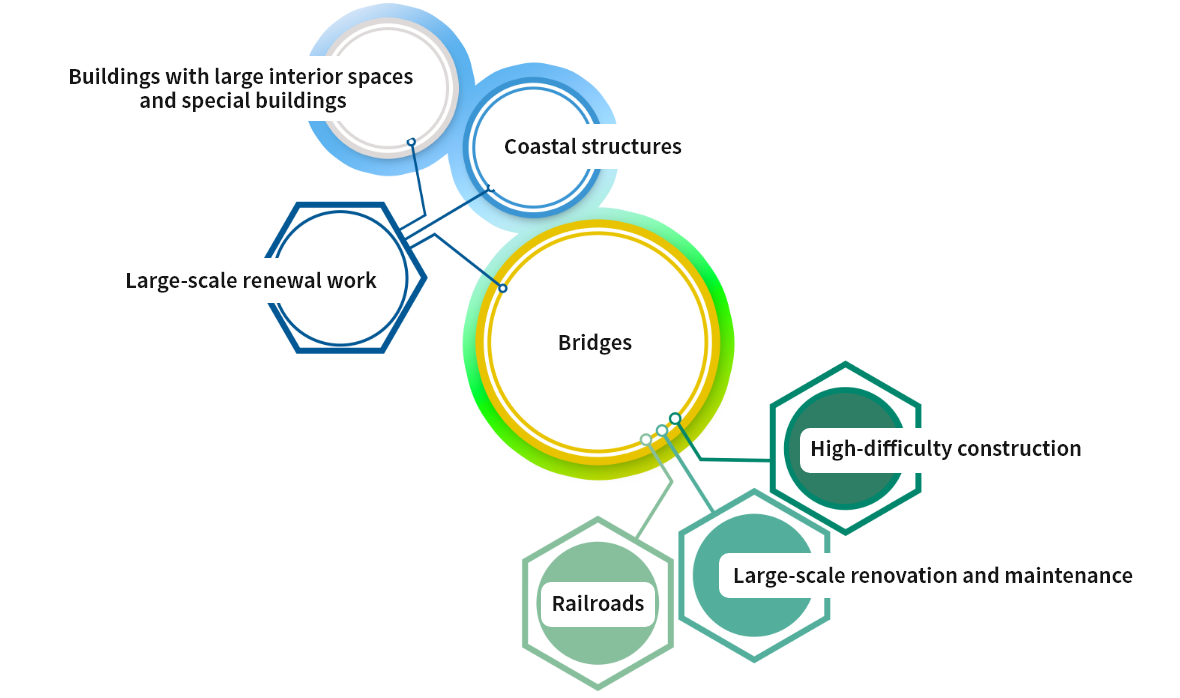
Large-space and specialized buildings
Coastal structures
Bridges
High-difficulty construction
New bridges, including large projects
Large-scale renovation and maintenance
Railroads
Actual Results for the Fiscal Year Ended March 31, 2023
Net sale
¥60,279million
Operating profit
¥5,127million
Profit attributable to owners of parent
¥3,077million
ROE
8.9%
ROA
8.6%
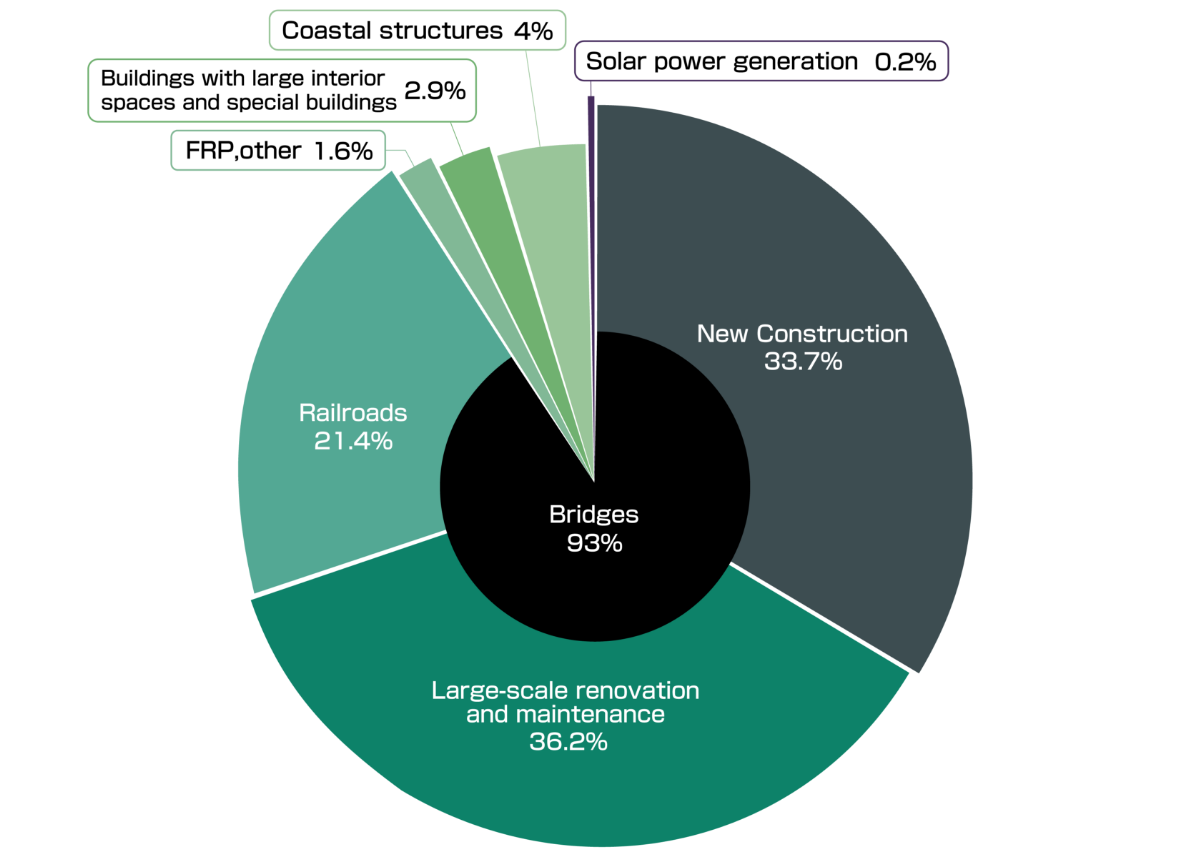
FY2023 Sales composition by business segment
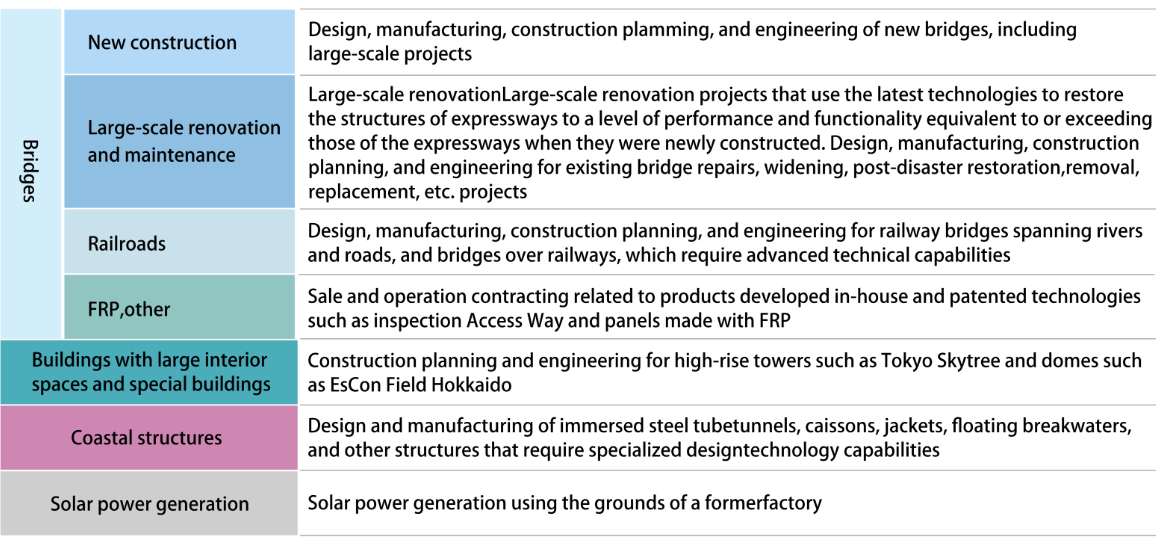
Major Past Project
We have contributed to society while supporting safe and convenient lifestyles through projects that have greatly contributed to the development of the bridge business, as well as construction and maintenance. Here are some of our representative projects.
-
beginning
-
Present
A project that made significant contributions to the bridge construction industry Edobashi Junction
We tackled the challenges of complex designs,
confined spaces, and building over a flowing river to construct this highway junction.
Symbol of reconstruction from the Great East Japan Earthquake Kanae Bridge(Kesennuma Bay Bridge)
The sea-spanning portion of this bridge is the Tohoku region's largest cable-stayed bridge
A project that made significant contributions to the bridge construction industry Edobashi Junction
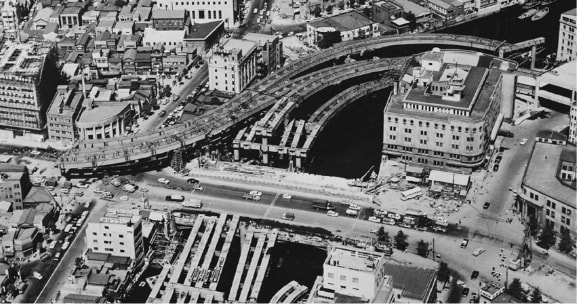
We tackled the challenges of complex designs, confined spaces, and building over a flowing river to construct this highway junction.
The project was an extraordinarily difficult one, involving a complex rigid-frame structure* of curved girders and construction work performed over a narrow river and the heavily-trafficked Nihonbashi and Edobashi bridges.
* Rigid-frame structure: Normally, bridge beams are placed on top of bridge piers, but with rigid-frame structure construction the bridge piers and rigid couplings are integrated. This requires complex analysis of how force is transmitted through the structure.
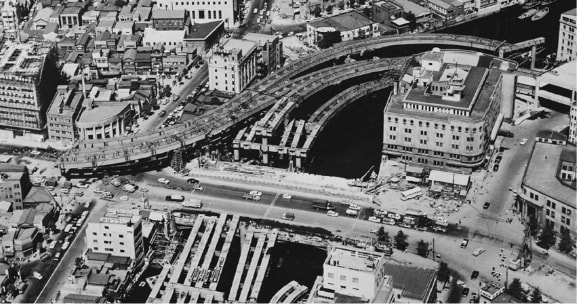
Project overview
This project was carried out as part of the Metropolitan Expressway infrastructure development performed in preparation for the Tokyo Olympic Games of 1964.
Traffic volume was rising rapidly at the time, and delays in the development of roads had resulted in chronic traffic jams. This project sought to alleviate these problems.
The project had a strict deadline: it needed to be completed during the five-year period leading up to the Tokyo Olympics.
Main topics
- 01 Stress analysis, design, and fabrication of complex three-dimensional rigid coupling structures and curved girders
- 02 Erection over a narrow river
- 03 Erection over the long-span Edobashi Bridge and the highly trafficked Nihonbashi Bridge
Tackling challenges
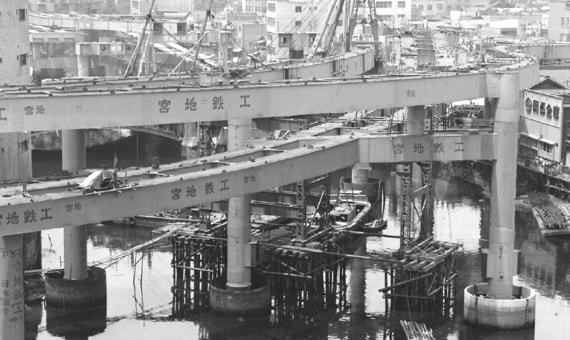
Erection over a narrow river
Stress analysis, design, and fabrication of complex three-dimensional rigid coupling structures and curved girders
We used electronic computers, a rarity at the time, to perform stress calculations. We performed model testing and examined many aspects of the project, such as fabrication methods including welding techniques. We also conducted research and development regarding welding technologies, quality management, and more.
Temporary assembly was performed in advance and the manufacturing precision was confirmed.
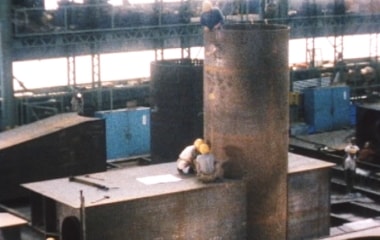
Corner fabrication (column base and transverse beam)
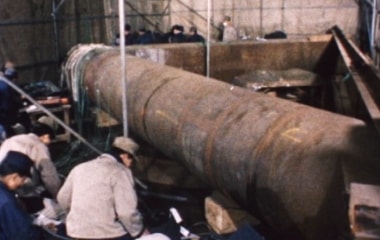
Internal stress measurement using a 1/2 scale model (model testing)
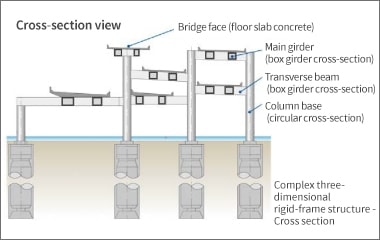
Complex three-dimensional rigid-frame structure - Cross section
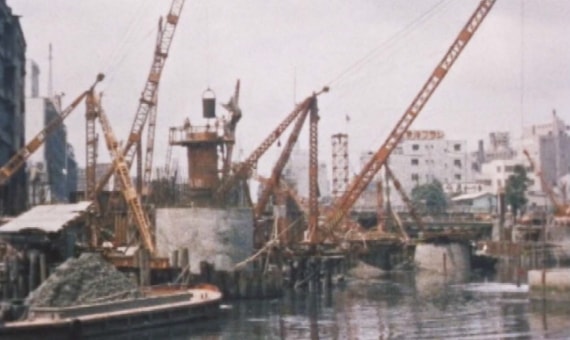
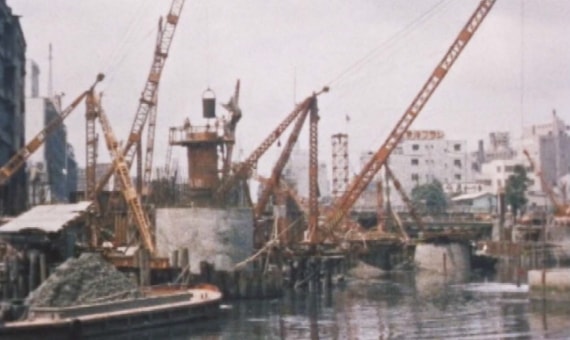
Erection over a narrow river
Because the construction was performed over a narrow river, bridge components such as the anchor frame, bridge piers, transverse beams, and main girders were transported via barge and floating cranes and lifting equipment were used to put the components in place.
「Floating crane erection method」 + Large block hoisting and erection method
Floating crane erection method
We used a 35 ton floating crane, developed in-house, to erect the anchor frame, bridge piers, bridge beams, and other components.
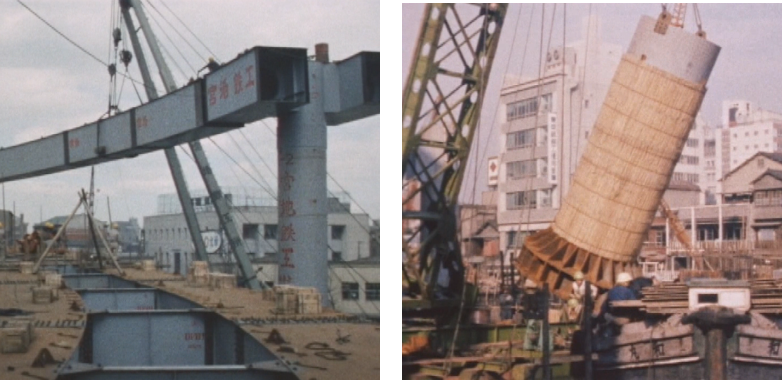
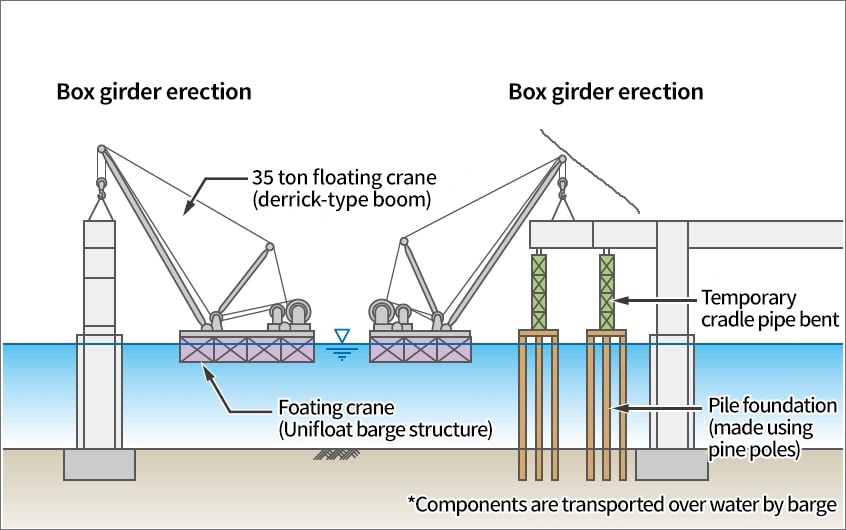
Large block hoisting and erection method
A floating crane was used to assemble the bridge beams into large blocks on a connected multi-section unifloat barge. A gantry special hoisting machine installed on the top of a main girder in advance then hoisted and placed the blocks.
The project involved numerous construction restrictions. The elevated bridge was to be erected on a narrow river, passing over the Edobashi Bridge, which is not only a long-span structure but which also has a complex junction design, and over the Nihonbashi Bridge, which has a high traffic volume. We used various techniques to address these problems.
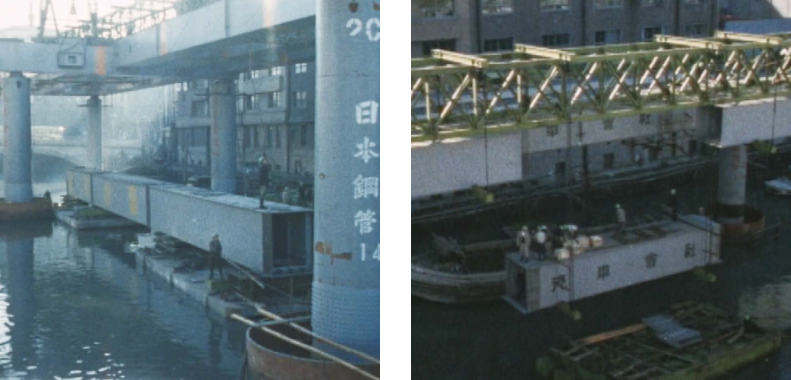
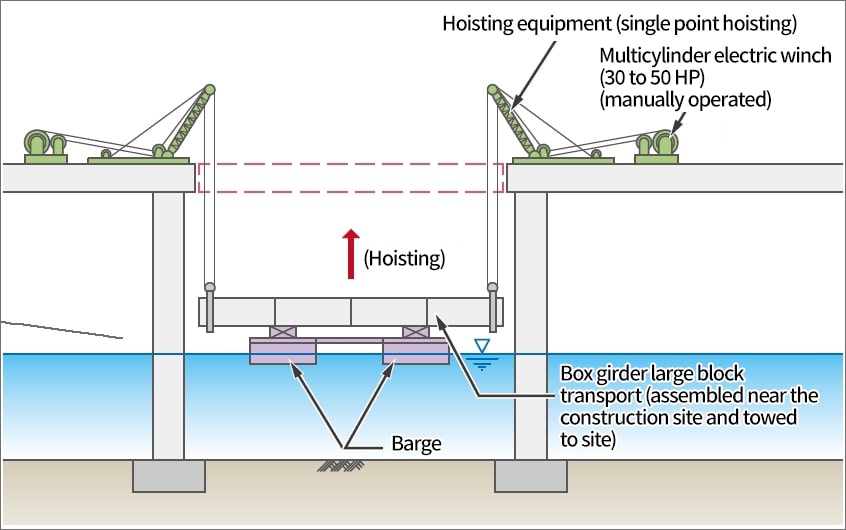
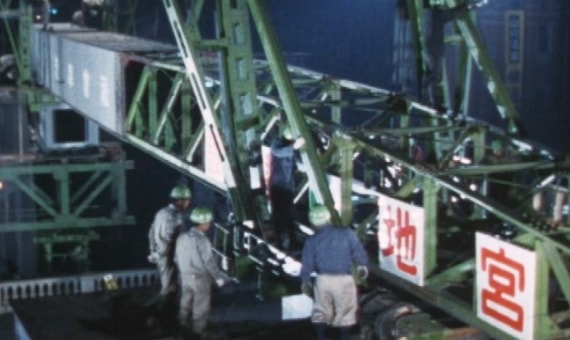
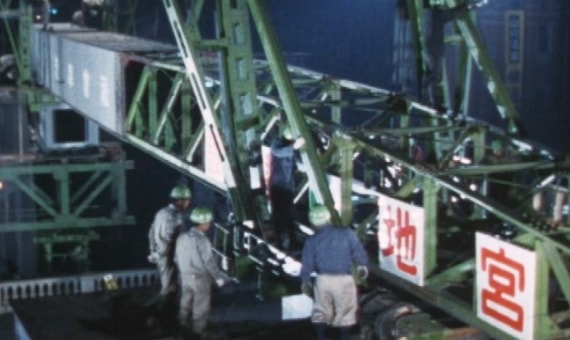
Erection over the long-span Edobashi Bridge and the highly trafficked Nihonbashi Bridge
We attached launching equipment (28 meters long) with a truss structure we developed in-house to the ends of bridge beams erected on bogies on rails installed on the tops of beams on both sides, and then used winches to erect the structure over the heavily trafficked Nihonbashi Bridge to draw and send structural components. The transported bridge beams were placed in position by lowering equipment capable of supporting 30 ton loads.
「Temporary cradle bent & cable crane erection method」 + Launching election method with launching girder
Temporary cradle bent & cable crane erection method
The girders installed high above Edobashi Bridge involved a complex structure involving a multistory arrangement of inbound, outbound, and branching lines, so the cable crane erection method was used. This method required a temporary cradle bent to be constructed over Edobashi Bridge. However, Edobashi Bridge itself would not be sufficiently strong to support it, so instead erection trusses were installed on the pedestrian walkways on both sides to disperse the reaction forces.
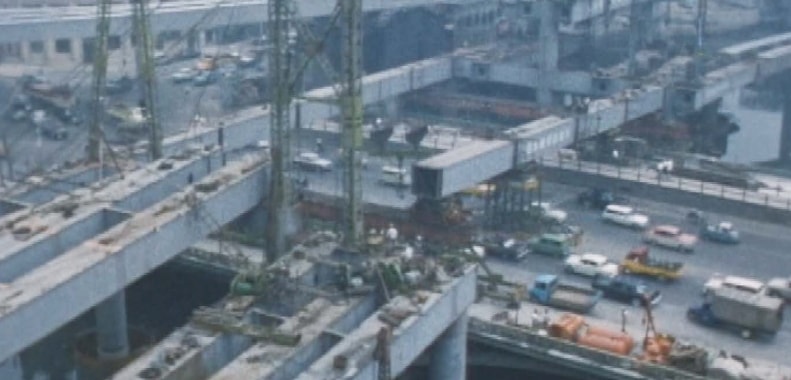
Bridge erection
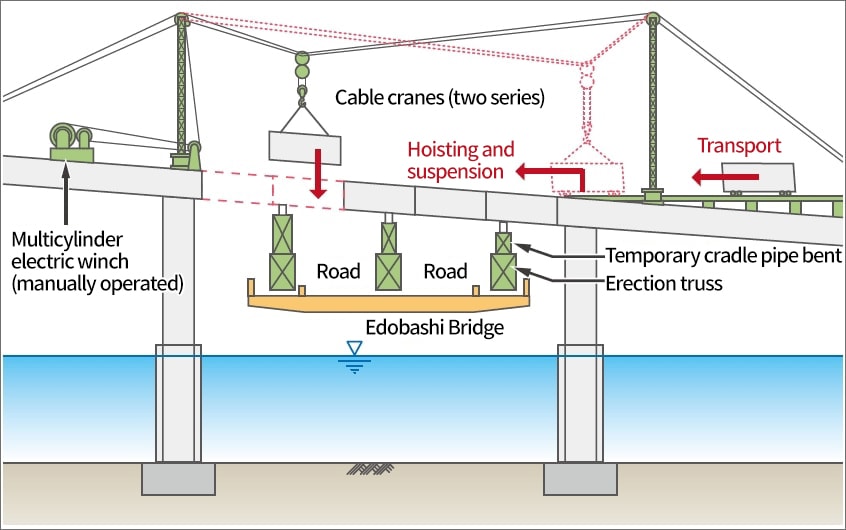
手延べ式送り出し工法
橋げたの先に取り付けた「手のべ機」を使ってバランスをとりながら、向こう岸まで橋げたを送り出す方法です。
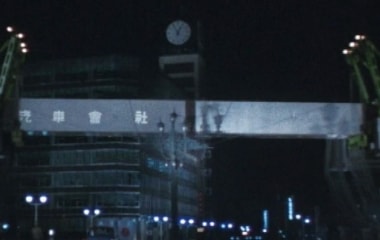
Lowering situation
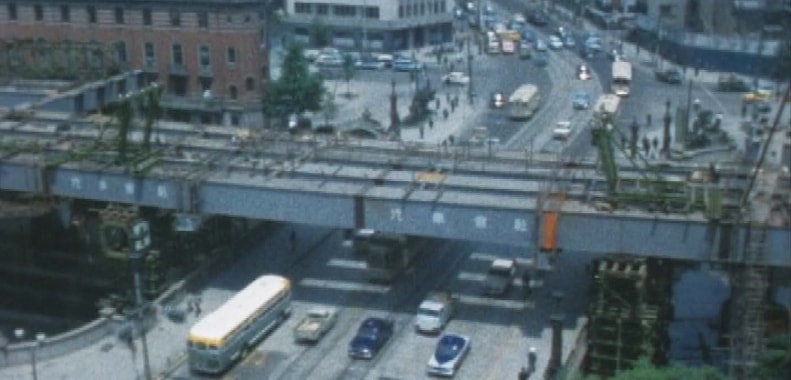
Closing situation
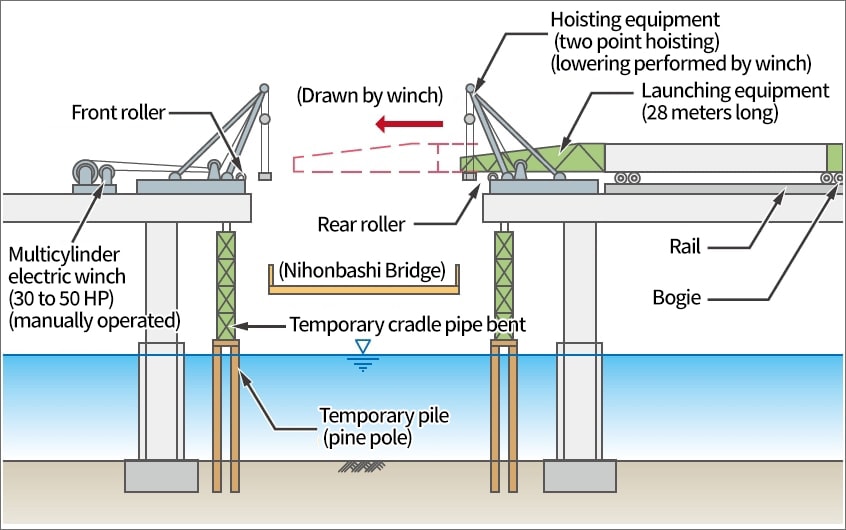
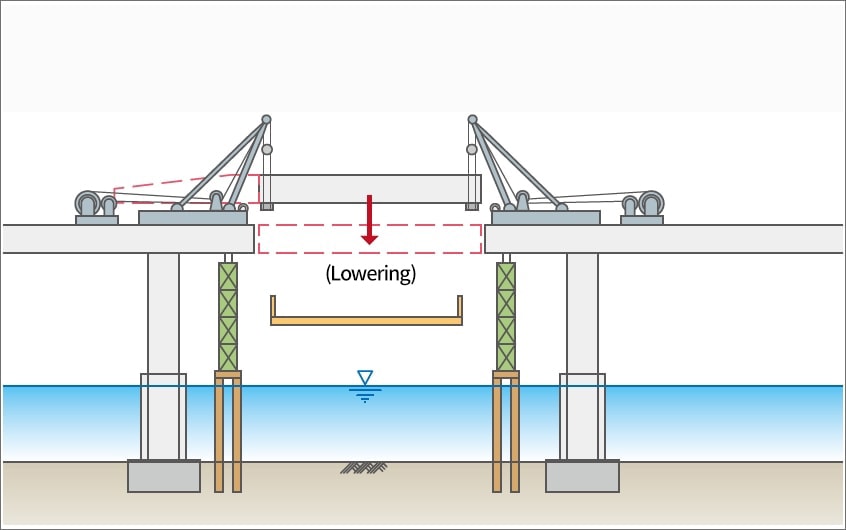
Symbol of reconstruction from the Great East Japan Earthquake Kanae Bridge(Kesennuma Bay Bridge)
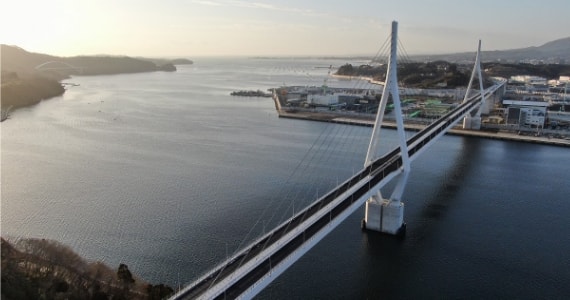
The sea-spanning portion of this bridge is the Tohoku region's largest cable-stayed bridge*
* Cable-stayed bridge: A bridge shape in which diagonal lines stretching from towers are directly connected to bridge beams, supporting them
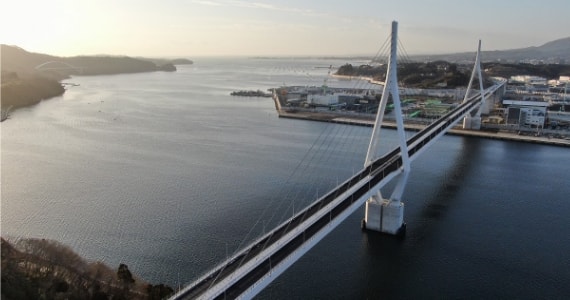
Project overview
The Kanae Bridge (Kesennuma Bay Bridge) was erected across Kesennuma Bay on the Sanriku Expressway. The Kogoshio area project, on which our Group worked, was a difficult construction project primarily consisting of special bridge erection work. In May 2019, we erected the large blocks of the main tower, and then from July we proceeded to erect stiffening girders. In May 2020, we erected the block that linked the Kogoshio area structure to the adjacent Asahi area structure. 迫力ある架設動画をお楽しみ下さい。
Highlights of the bridge erection video
0'40": Erection of the main tower large block
1'40": Erection of the main girder large block
2'20": Erection of the main girder cycle
4'12": Erection of the main girder closing block
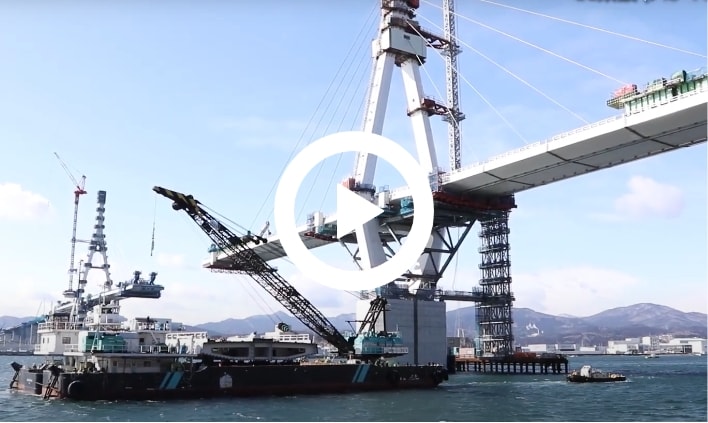
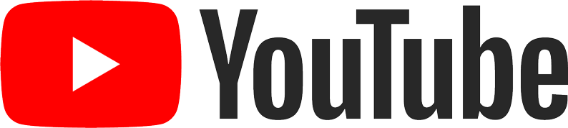
Also be sure to take a look at the official MIYAJI ENGINEERING GROUP YouTube channel.
「フローティングクレーン工法」、「大ブロック吊り上げ工法」、
「ケーブルクレーン工法」、「手延べ式送り出し工法」などは、
現在の一般的な架設工法の原型となり、現在に受け継がれています。